引言
UNS N08926镍基合金是一种高性能耐腐蚀合金,广泛应用于化工、石油和海洋工程等领域。它不仅具有出色的耐腐蚀性,尤其是在酸性环境中的抗点蚀、抗缝隙腐蚀性能,而且在高温下展现出良好的机械性能。合金的断裂性能是影响其使用寿命和可靠性的重要因素,因此对于UNS N08926镍基合金的断裂性能的研究尤为关键。本文将从断裂强度、断裂韧性、疲劳裂纹扩展以及环境对其断裂性能的影响等角度,详细阐述UNS N08926镍基合金的断裂性能表现,并结合相关实验数据与实际应用案例,深入探讨如何优化该合金的断裂性能以适应不同工业领域的需求。
UNS N08926镍基合金的断裂性能分析
断裂强度
UNS N08926镍基合金的断裂强度是衡量其承受外力作用时抵抗断裂能力的主要指标。合金的微观组织、热处理工艺和加载方式对其断裂强度有直接影响。研究表明,UNS N08926的抗拉强度可达到650 MPa左右,在中高温环境下仍能保持较高的断裂强度。这种性能主要得益于镍基合金独特的微观结构,其含有的高铬、高钼和铜元素共同作用,有效提高了合金的抗断裂能力。
在高温高压的苛刻环境下,UNS N08926合金表现出良好的蠕变断裂强度,特别是在700℃以上的环境中,长期服役也能保持稳定的强度。这使得其在高温设备和化工换热器等关键部件中具有广泛的应用潜力。
断裂韧性
断裂韧性是衡量材料在受力断裂过程中吸收能量的能力,是材料延展性和抗脆断性能的关键指标。UNS N08926镍基合金凭借其韧性,在严苛的工业环境中表现出卓越的断裂韧性。实验数据显示,经过优化的热处理后,该合金的断裂韧性显著提升,特别是在低温环境中,其韧性表现优异,能够有效抵抗低温脆性断裂。
通常,镍基合金的韧性与其内部显微组织密切相关,UNS N08926合金的高镍含量使其具有良好的晶粒结构和较高的相变温度,这在一定程度上提高了其在低温及冲击载荷下的断裂韧性。
疲劳裂纹扩展行为
在实际应用中,材料常常受到循环载荷的作用,疲劳裂纹扩展行为对UNS N08926合金的断裂性能有重要影响。疲劳裂纹的扩展速率决定了材料的疲劳寿命,而UNS N08926合金凭借其优异的抗疲劳性能,在多次循环载荷作用下仍能保持较长的疲劳寿命。
根据相关实验数据,在100 MPa的应力强度因子范围内,UNS N08926的疲劳裂纹扩展速率相对较低,这得益于其较高的铬、钼含量和稳定的微观组织结构。通过合理的表面处理工艺,如表面淬火和喷丸处理,可以进一步减少疲劳裂纹的扩展,提高其抗疲劳断裂性能。
环境因素对断裂性能的影响
环境条件对于UNS N08926镍基合金的断裂性能影响显著,特别是在腐蚀环境中,合金的断裂行为复杂。研究表明,在酸性介质中,UNS N08926合金表现出优异的抗应力腐蚀开裂(SCC)性能。这种性能主要依赖于合金中镍、铬和钼元素的协同作用,这些元素能够在表面形成致密的氧化膜,阻止腐蚀物质进入合金内部,从而降低了应力腐蚀开裂的可能性。
在高氯离子环境中,如果合金表面氧化膜破损,可能会加速点蚀或缝隙腐蚀,从而影响断裂性能。因此,在实际应用中,需结合具体的环境条件,采取适当的防护措施,如表面涂层或阴极保护,以确保合金的断裂性能不受恶劣环境的显著影响。
实际应用案例
在实际应用中,UNS N08926镍基合金常用于石油和天然气工业中的酸性气体处理设备。某海上钻井平台的脱硫装置中,UNS N08926合金在高温、高压及高硫化氢浓度的腐蚀环境中,服役10年后依然保持了较好的机械性能和抗断裂性能,设备运转稳定,未发生任何因断裂引发的事故。这一案例充分说明了UNS N08926镍基合金在恶劣工况下的优异断裂性能,为类似设备的设计和选材提供了重要参考。
结论
UNS N08926镍基合金凭借其出色的断裂强度、断裂韧性以及抗疲劳裂纹扩展性能,在化工、石油和海洋工程等领域发挥了重要作用。其在高温、高压及腐蚀环境下的稳定表现,使得它成为苛刻工况中理想的材料选择。通过优化热处理工艺及采取适当的防护措施,进一步提升UNS N08926镍基合金的断裂性能,对于延长设备使用寿命、提高工业安全性具有重要意义。
因此,对于涉及高温、腐蚀和应力交变的关键设备和结构,UNS N08926镍基合金无疑是非常可靠的选择。随着科技的进步和新材料加工技术的发展,UNS N08926的断裂性能将得到进一步优化,应用前景也会更加广阔。
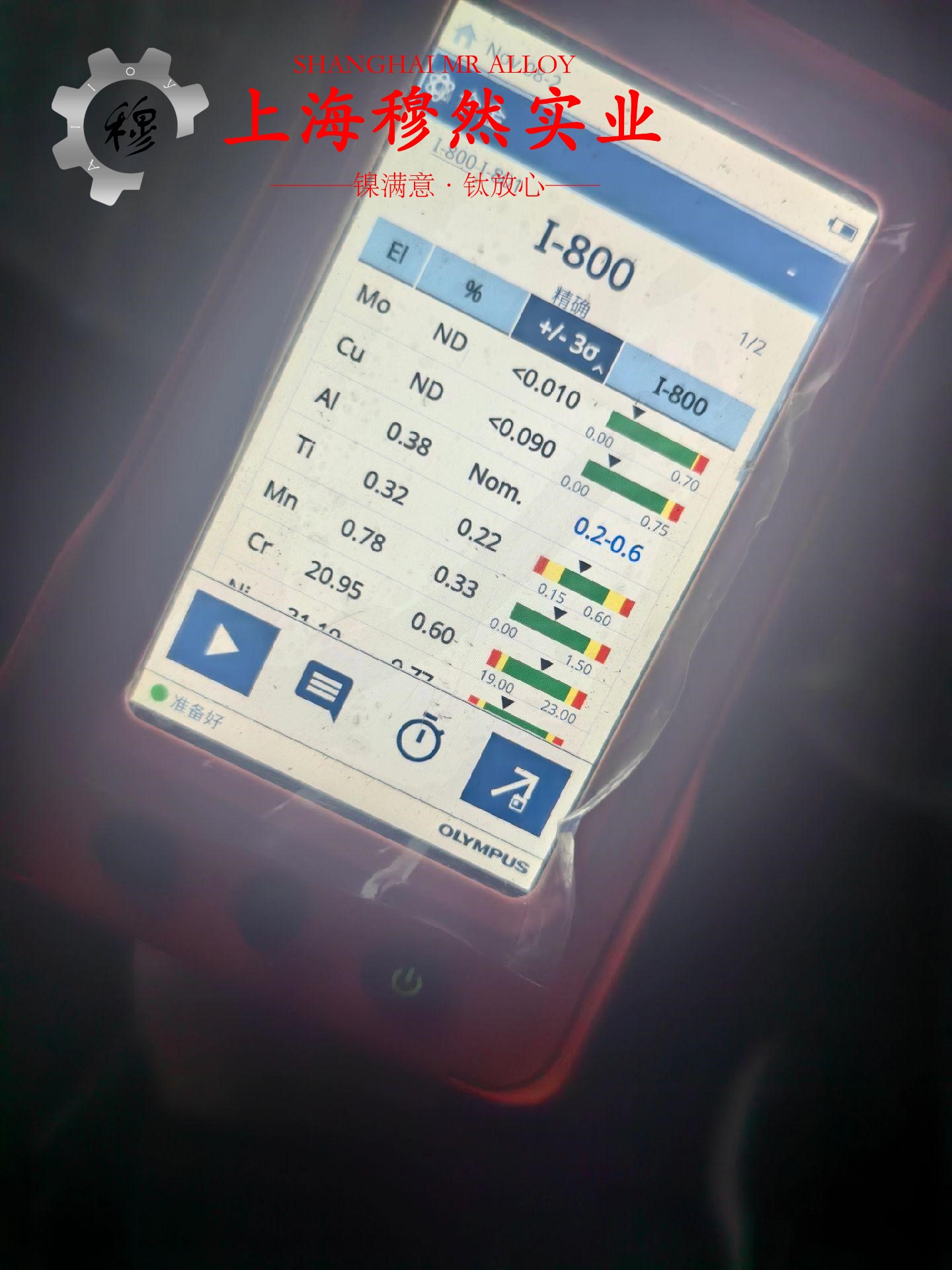
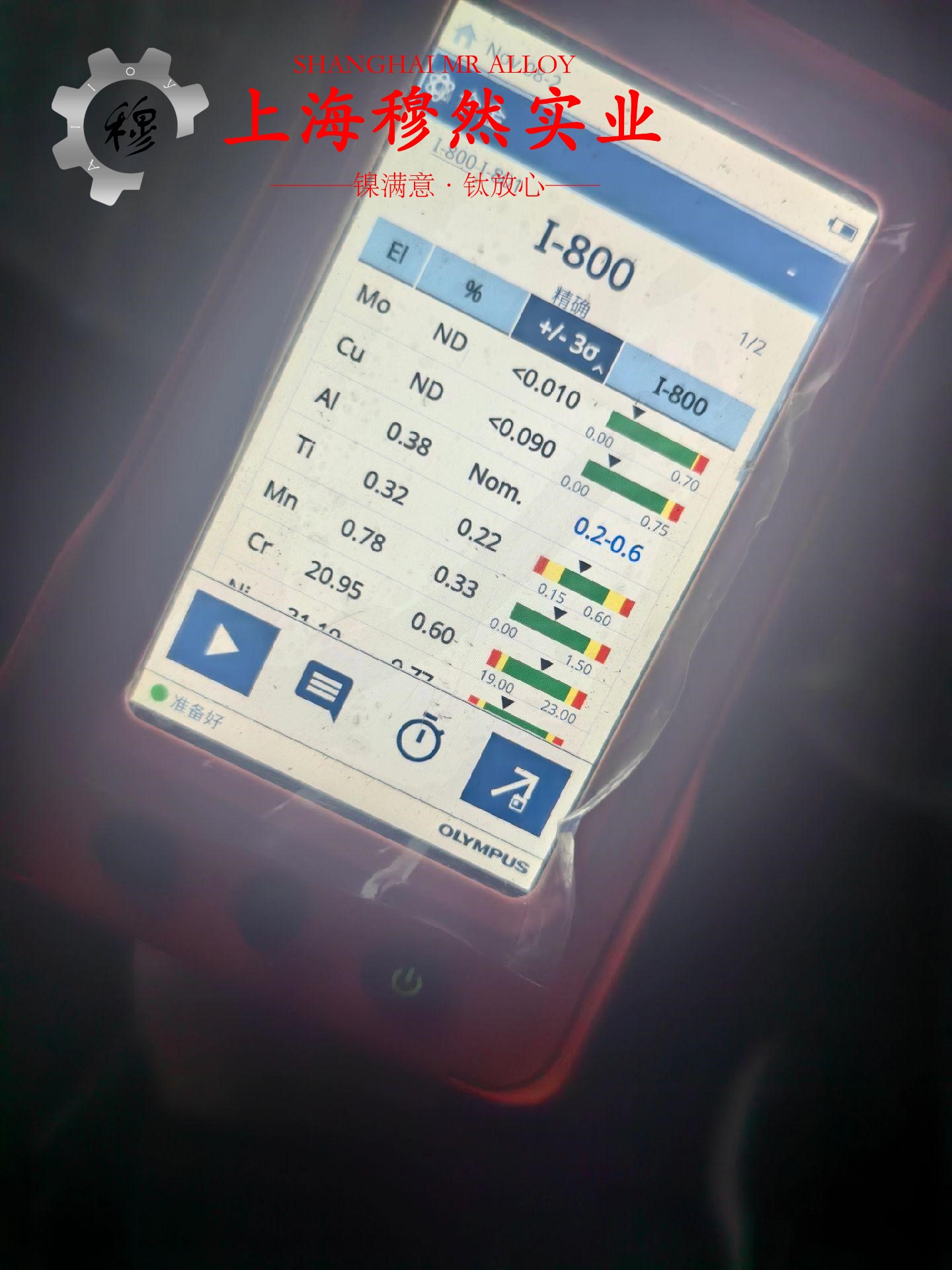