Ni77Mo4Cu5高初磁导率合金零件热处理工艺综述
引言
Ni77Mo4Cu5合金是一种典型的高初磁导率合金,广泛应用于电子、通讯等高精度磁性元件的制造。其核心特点是具备优异的磁导率和良好的稳定性,适用于需要精确控制磁性能的器件。为了确保该合金的性能能够在实际应用中达到最佳效果,热处理工艺成为了制备过程中至关重要的一环。本文将详细综述Ni77Mo4Cu5高初磁导率合金的零件热处理工艺,探讨热处理参数对合金性能的影响,并结合相关案例分析优化的热处理方法。
正文
1. Ni77Mo4Cu5高初磁导率合金的基本特性
Ni77Mo4Cu5合金的主要成分为77%的镍(Ni)、4%的钼(Mo)和5%的铜(Cu),该配比使其在常温下拥有非常高的初始磁导率。初始磁导率是衡量磁性材料在低磁场下表现的关键参数,这直接关系到合金在电感元件、磁芯等高性能应用中的表现。钼的加入可以显著提高合金的磁导率和稳定性,而铜则有助于改善材料的机械加工性能。
尽管Ni77Mo4Cu5合金本身具有良好的磁性特征,合理的热处理工艺可以进一步改善其磁性能、降低内应力并提高结构均匀性。因此,掌握该合金的热处理技术对其最终性能具有重大影响。
2. 热处理工艺在Ni77Mo4Cu5合金中的重要性
热处理工艺在Ni77Mo4Cu5合金制造中起着关键作用,具体包括退火、淬火和回火等步骤。每一步的处理条件,如温度、时间及冷却方式等,都会显著影响合金的微观结构,从而影响其磁性能。合理的热处理可以有效降低材料中的内应力,优化晶粒大小,进而提升初磁导率和其它关键性能。
退火
退火是Ni77Mo4Cu5合金热处理的关键步骤,其目的是使材料在高温下保持足够的时间以恢复组织的均匀性,减少内应力,改善材料的塑性和韧性。通常,Ni77Mo4Cu5合金的退火温度控制在600℃至900℃之间。过高的退火温度可能会导致晶粒粗化,影响磁导率,而过低的温度则无法充分释放内应力。实际应用中,合金的退火时间一般控制在2至4小时,以确保晶粒适当长大而不会出现粗化现象。
淬火
淬火是通过快速冷却的方法将材料从高温急速降温,抑制合金内部组织的析出和相变。对于Ni77Mo4Cu5合金,淬火有助于形成较为理想的磁畴结构,从而提高初磁导率。但淬火工艺必须精确控制,因为过快的冷却速率可能会引发材料裂纹或导致晶粒结构不均匀,反而降低其性能。
回火
回火是Ni77Mo4Cu5合金热处理中的重要补充步骤,通常在淬火后进行。通过将淬火后的合金加热至适中的温度并保温一段时间,回火能够释放淬火过程中残留的内应力,并进一步改善材料的韧性和塑性。一般情况下,回火温度控制在200℃至400℃之间,时间则根据实际需要调整。适当的回火可以显著提高Ni77Mo4Cu5合金的磁导率,同时减少晶界中的缺陷,提高材料的长期使用稳定性。
3. 热处理工艺对Ni77Mo4Cu5高初磁导率合金性能的影响
大量研究表明,热处理参数的选择对Ni77Mo4Cu5合金的最终性能影响显著。例如,在合理的退火温度下,晶粒结构均匀,内应力释放充分,磁导率能够达到其理想状态。相反,过高或过低的退火温度都会导致晶粒尺寸的不均匀,进而影响磁性性能。
晶粒尺寸与磁导率
热处理通过影响晶粒尺寸和相界面分布直接决定了Ni77Mo4Cu5合金的磁性能。过大的晶粒会降低初磁导率,而过小的晶粒则可能导致材料在高频应用中出现涡流损耗。因此,在热处理工艺中,控制晶粒大小的均匀性尤为重要。通过优化退火和回火工艺,可以得到适宜的晶粒结构,提升合金的综合性能。
内应力的消除
退火和回火是消除内应力的有效途径。研究表明,内应力会影响磁畴的运动,从而影响磁导率。适当的热处理可以降低材料内部的残余应力,改善磁性元件在工作环境中的稳定性和使用寿命。
4. 典型案例分析
在实际应用中,通过对Ni77Mo4Cu5合金零件进行科学的热处理工艺设计,磁性元件的性能得到了显著提升。例如,某知名电子元件制造商在生产变压器磁芯时,采用了600℃退火、快速冷却、并在250℃回火2小时的工艺,最终获得了极佳的磁导率和稳定性。在电感元件的制造中,通过调整回火温度和时间,使得合金的磁性能得到了进一步优化,显著降低了高频下的磁损耗。
结论
Ni77Mo4Cu5高初磁导率合金的零件热处理工艺对其性能表现具有重要影响。合理的退火、淬火和回火工艺可以显著提升合金的磁导率、降低内应力并改善其微观结构。通过优化热处理参数,能够进一步释放Ni77Mo4Cu5合金的潜力,满足高精度磁性元件的需求。随着技术的不断进步,Ni77Mo4Cu5合金的热处理工艺将会进一步完善,为高性能磁性材料的开发提供更为强大的支持。
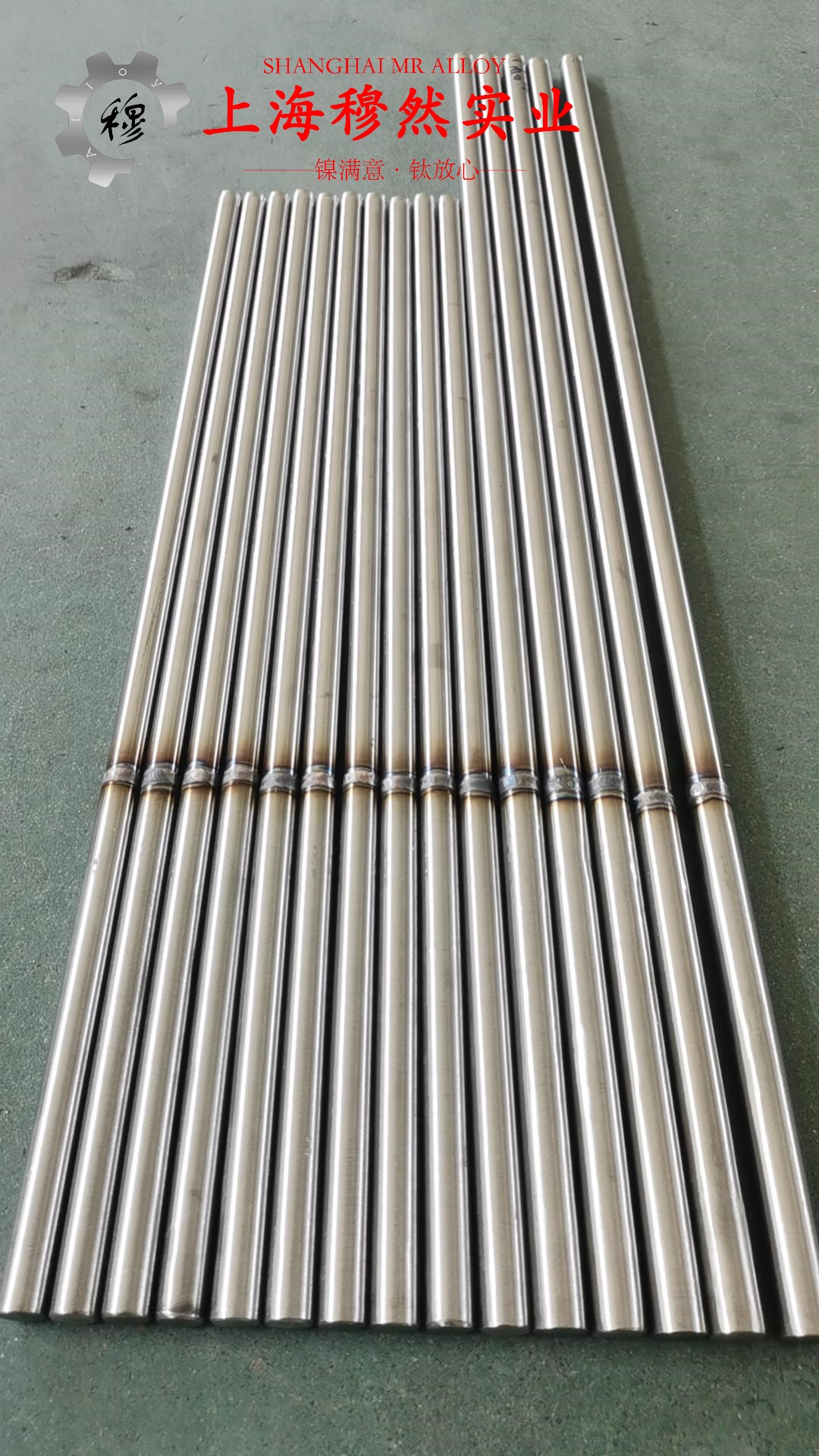
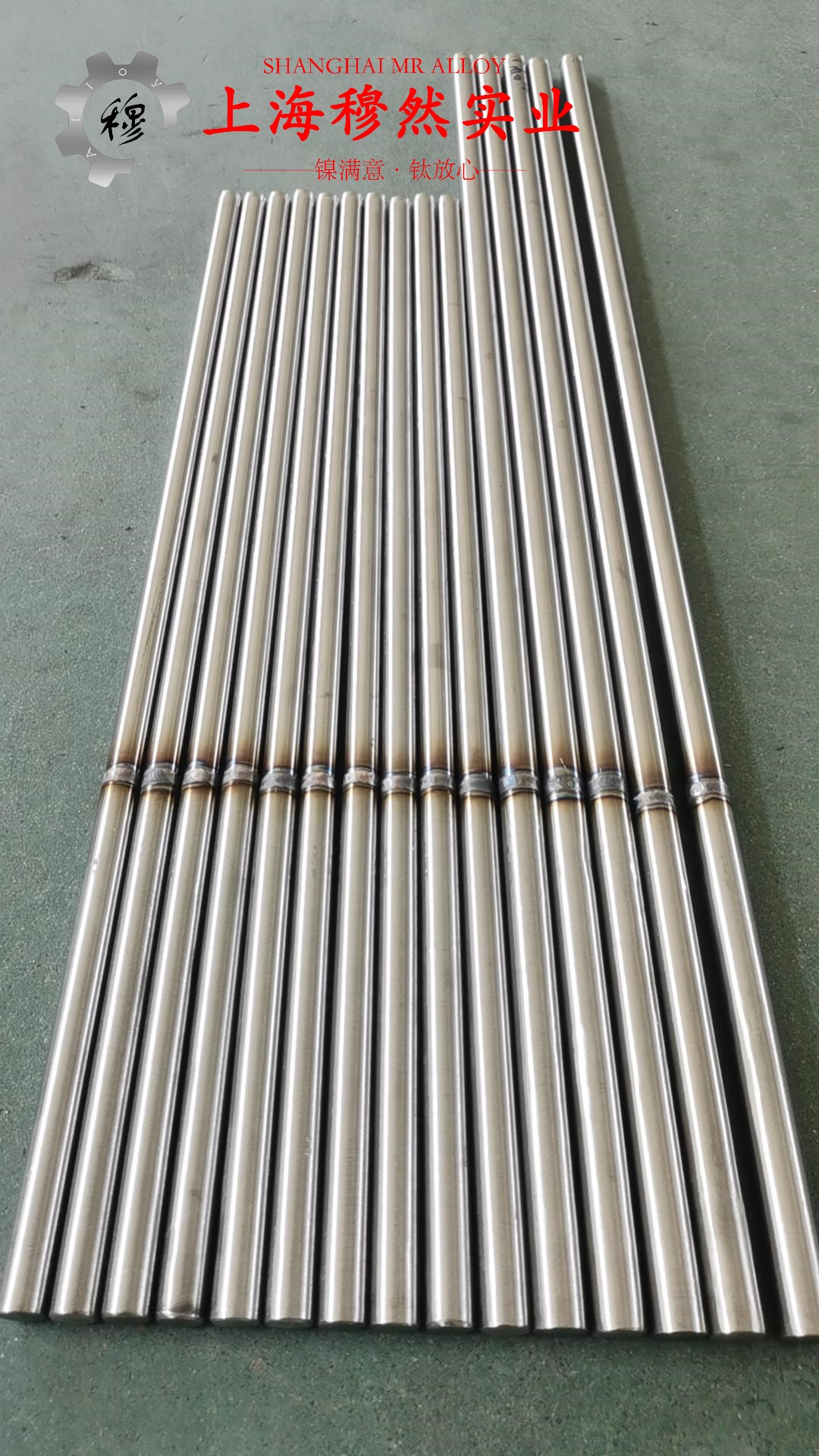