4J32合金的熔炼与铸造工艺阐释
引言
4J32合金是一种铁镍合金,因其在低温条件下具备高稳定性、低热膨胀系数等优异性能,被广泛应用于航天、仪器仪表和精密设备等领域。4J32合金的加工难度较高,尤其是在熔炼与铸造过程中,对工艺控制有较高要求。这篇文章将深入探讨4J32合金的熔炼与铸造工艺,分析各工艺环节对材料性能的影响,提供相关数据与案例来解释如何通过优化工艺流程,提升4J32合金的质量与生产效率。
1. 4J32合金的熔炼工艺
1.1 材料准备与清理
4J32合金的熔炼首先需要准备好纯净的原料。主要成分为铁、镍和钴,原料的纯度对合金的最终性能至关重要。为了确保熔炼过程中的元素成分不受污染,通常选用真空感应熔炼(VIM)或真空电弧重熔(VAR)工艺。真空环境下的熔炼可以避免杂质元素(如氧、氢、氮等)进入材料,从而提高合金的纯净度和机械性能。
在正式熔炼之前,所有原料必须进行清理处理,尤其是金属表面的氧化皮、油污等。清洁过程对合金纯度尤为关键,因为任何污染物的残留都会影响熔炼后的微观组织。
1.2 熔炼工艺控制
在4J32的熔炼过程中,温度控制是最重要的参数之一。熔炼温度的设置需要严格控制在1550℃-1650℃之间。如果温度过高,可能导致金属中某些元素挥发,如镍的损失;温度过低则可能导致熔体流动性不佳,无法充分融合各成分。4J32熔炼过程中还需使用氩气或真空环境,避免空气中的氧气和氮气进入金属,形成气孔、夹杂等缺陷。
1.3 精炼技术
为了进一步减少合金中的气体含量以及杂质颗粒,熔炼后通常需要进行精炼处理。常用的技术包括电渣重熔(ESR)和真空重熔(VAR)。精炼的主要目的是通过控制凝固过程中的结晶条件,减少材料内部的偏析现象,使合金的晶粒更加均匀细小,提升材料的强度和韧性。
2. 4J32合金的铸造工艺
2.1 铸造模具的设计与准备
4J32合金铸造过程中,模具的设计至关重要。由于4J32具有低膨胀系数,模具材料必须选择与4J32合金热膨胀特性相匹配的材料。通常,铸造模具会使用石墨模具或陶瓷模具,以保证铸造过程中合金冷却和凝固的稳定性。
为了提高铸件的表面质量,在模具制作完成后,需对其进行表面处理,确保模具表面光滑无缺陷。这一步骤有助于减少铸造过程中产生的表面瑕疵,并提高4J32合金的外观质量。
2.2 铸造工艺参数的控制
铸造过程中,浇注温度、浇注速度和冷却速率都是关键参数。4J32合金的浇注温度一般控制在1550℃左右,较高的浇注温度可以提高金属液的流动性,减少铸件内部的缩孔与裂纹。过高的浇注温度可能导致过度氧化,进而形成夹杂物,因此必须保持温度在适当范围内。
冷却速率则对4J32的微观组织有重要影响。过快的冷却速度可能会导致热应力过大,形成裂纹;过慢的冷却速度又可能引发晶粒粗大,降低合金的力学性能。因此,通常采用分阶段冷却的方式,逐步降低温度,以减少热应力并优化晶粒尺寸。
2.3 铸造缺陷的防控
铸造缺陷如缩孔、夹杂物、气孔等是4J32铸造过程中常见的问题。为防止这些缺陷的产生,需在铸造前进行充分的排气处理,确保模具和熔体中的气体含量控制在极低水平。在浇注过程中应保持恒定的流速,避免湍流形成夹杂。
使用无氧铜等材料作为排气导流件,可以有效改善模具内气体的流通性,减少气孔的产生。采用磁力搅拌技术也能促进金属液的均匀性,减少偏析和夹杂的形成。
3. 4J32熔炼与铸造工艺的优化与应用案例
3.1 工艺优化
近年来,随着4J32应用领域的扩大,研究人员不断致力于优化熔炼与铸造工艺。通过引入先进的计算机数值模拟技术,可以更精确地预测铸造过程中合金的流动行为和冷却情况。这种模拟技术不仅能优化工艺参数,还能减少试验成本,提高生产效率。
3.2 成功应用案例
在某航天器精密零部件的制造过程中,应用了先进的4J32熔炼与铸造技术,最终产品具备高耐热性、低膨胀系数,完全满足了航天环境中的严苛要求。通过采用真空熔炼结合电渣重熔的工艺路线,有效降低了合金中的氧含量,使得零部件在超低温条件下依然能保持良好的机械性能。这一案例充分说明了优化4J32熔炼与铸造工艺的必要性和重要性。
结论
4J32合金的熔炼与铸造工艺是其生产过程中最为关键的环节之一。通过合理控制熔炼温度、精炼工艺以及铸造参数,能够显著提升合金的物理性能和机械性能。随着新技术的引入,4J32合金的生产工艺将更加高效与精密,未来它将在更多领域得到广泛应用。针对这一合金的工艺研究依然具有很大的探索空间,推动4J32合金在高端制造业中的应用将具有重要的战略意义。
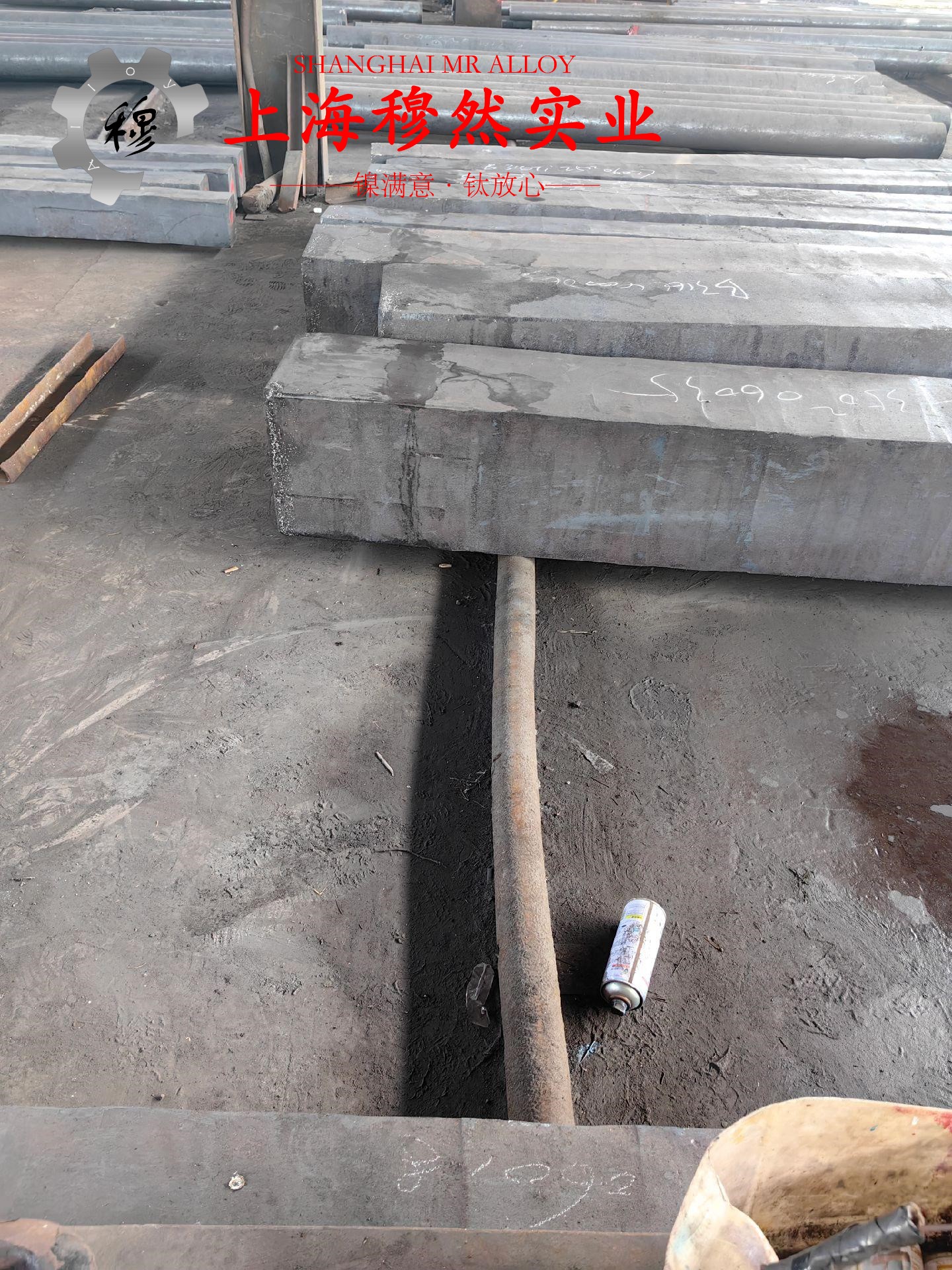
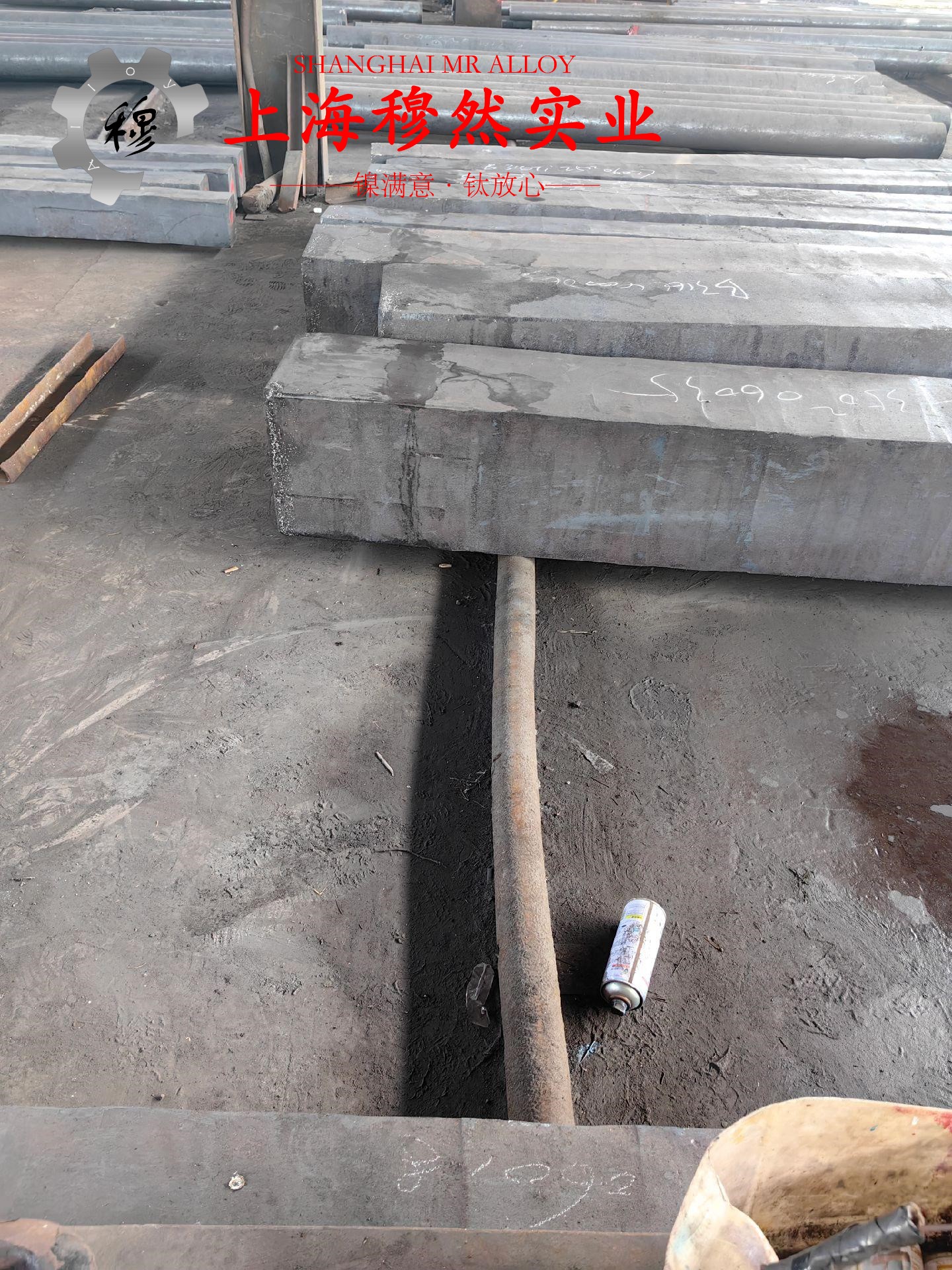