A286铁镍铬基高温合金表面处理工艺介绍
引言
A286铁镍铬基高温合金是一种广泛应用于航空航天、汽轮机、石油化工等高温、高压环境中的优质材料。这种合金因其优异的高温强度、抗氧化性以及耐腐蚀性能而备受青睐。在实际使用中,A286铁镍铬基高温合金的表面处理工艺对于提升其性能、延长使用寿命至关重要。本文将深入介绍A286铁镍铬基高温合金的各种表面处理工艺,探讨其应用和效果,帮助用户更好地理解和掌握该合金的表面处理技术。
正文
1. A286铁镍铬基高温合金表面处理的必要性
A286铁镍铬基高温合金在高温条件下具有良好的性能,但其表面在长期使用中仍然面临腐蚀、氧化、磨损等问题。为了提升合金的使用寿命和耐久性,表面处理工艺显得尤为重要。合理的表面处理不仅能增强材料的抗氧化和抗腐蚀能力,还能有效提高疲劳强度、减小摩擦系数,进而提升零件的整体性能。
2. 常见的A286铁镍铬基高温合金表面处理工艺
2.1. 电镀工艺
电镀是A286合金表面处理中的常用工艺之一,尤其适用于需要耐腐蚀、耐磨损的环境。在A286合金的表面电镀一层如镍、铬或铜等金属涂层,能大幅提高材料的抗腐蚀能力,同时减少高温下氧化膜的生成。
以镀镍为例,镍层不仅能够形成保护膜,还具有一定的自修复能力,适用于高温氧化环境。电镀工艺简单,易于实现大批量生产,但其厚度控制要求较高,需保证涂层均匀性。
2.2. 气相沉积工艺
气相沉积(CVD或PVD)是另一种常用于A286铁镍铬基高温合金的表面处理工艺,特别是在航空航天等高精度要求的领域。PVD(物理气相沉积)工艺通过将涂层材料蒸发成气体,再在真空环境中沉积到A286合金表面,形成耐磨、耐腐蚀的涂层。相比于电镀,PVD涂层更为致密且附着力更强,能够在极端环境下提供更加持久的保护。
CVD(化学气相沉积)则适用于更大尺寸或形状复杂的工件,通过在气相反应中生成固态涂层,提供了均匀性更好的涂层质量。气相沉积技术虽然成本相对较高,但在A286铁镍铬基高温合金的复杂应用场景中表现出了无可替代的优势。
2.3. 激光表面处理
激光表面处理是一种高能束表面改性技术,通过高功率激光束在A286合金表面快速扫描,使表面材料发生熔融或相变,形成致密的耐腐蚀层。该工艺不仅能显著提升合金的耐磨、抗疲劳能力,还能够减少表面缺陷、提高抗裂性。
激光表面处理的最大优势在于其精准度极高,能够处理复杂结构部件的局部区域。激光表面淬火和激光熔覆技术还能进一步提高A286合金的耐磨和耐腐蚀性能,适用于要求极高的航空发动机、汽轮机叶片等领域。
2.4. 氧化处理
氧化处理是通过控制A286铁镍铬基高温合金在特定环境下的氧化反应,生成一层致密的氧化物保护层。热氧化处理(如阳极氧化)能够显著提高合金的抗氧化性能,减少高温下氧化层的剥落,特别是在腐蚀性气体或高温盐类环境中效果显著。
氧化处理还能增强合金的耐磨损性能,并且工艺成本相对较低,是提升A286合金表面性能的经济型选择。
2.5. 喷涂工艺
热喷涂是一种通过将涂层材料加热至熔融状态,然后高速喷涂到A286合金表面的表面处理技术。常用的喷涂材料包括氧化铝、氧化铬以及陶瓷材料等。喷涂工艺能够有效增强A286合金的高温抗氧化性和耐腐蚀性,且涂层厚度可控,适用于复杂形状的工件。
相比于其他表面处理工艺,热喷涂在处理厚重件或尺寸较大的工件时具有显著的优势,广泛应用于汽轮机、航空发动机等高温设备中。
3. 表面处理效果评价及数据支持
表面处理工艺的效果通常通过以下几个指标进行评估:抗腐蚀性、抗氧化性、耐磨性以及附着力。根据相关实验数据显示,经过PVD处理后的A286铁镍铬基高温合金,其抗氧化性能在1000°C高温下提高了约30%,而经过热喷涂处理的合金,其抗腐蚀能力相较未处理的合金提高了近40%。
不同工艺的选择需要根据具体应用环境的要求进行。例如,在极端高温条件下,激光表面处理和PVD技术表现优异,而在腐蚀性气体环境中,电镀和氧化处理则更为经济实用。
结论
A286铁镍铬基高温合金作为一种性能优异的高温合金材料,其表面处理工艺的选择对于提升其在极端环境下的性能表现至关重要。从电镀、气相沉积、激光表面处理到热喷涂等工艺,每种表面处理技术各有其独特的优势,适用于不同的应用场景。用户在选择表面处理方法时,需结合工件的实际使用环境和性能要求,合理选择合适的表面处理工艺,以确保A286合金在高温、高压环境中的长效稳定性。
未来,随着表面处理技术的不断进步,A286铁镍铬基高温合金的应用潜力将进一步扩大,其在高端制造领域的表现也将愈发卓越。
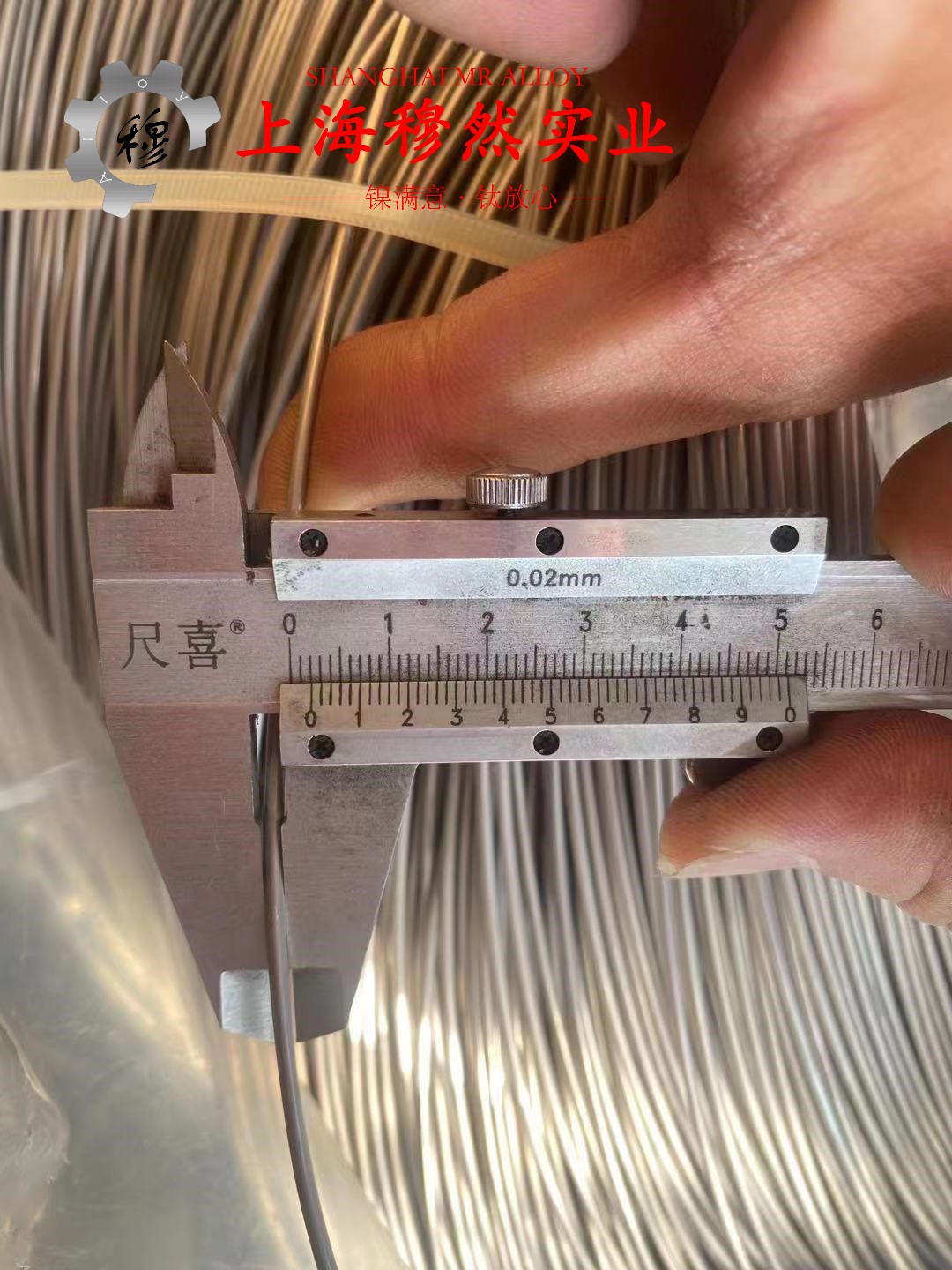
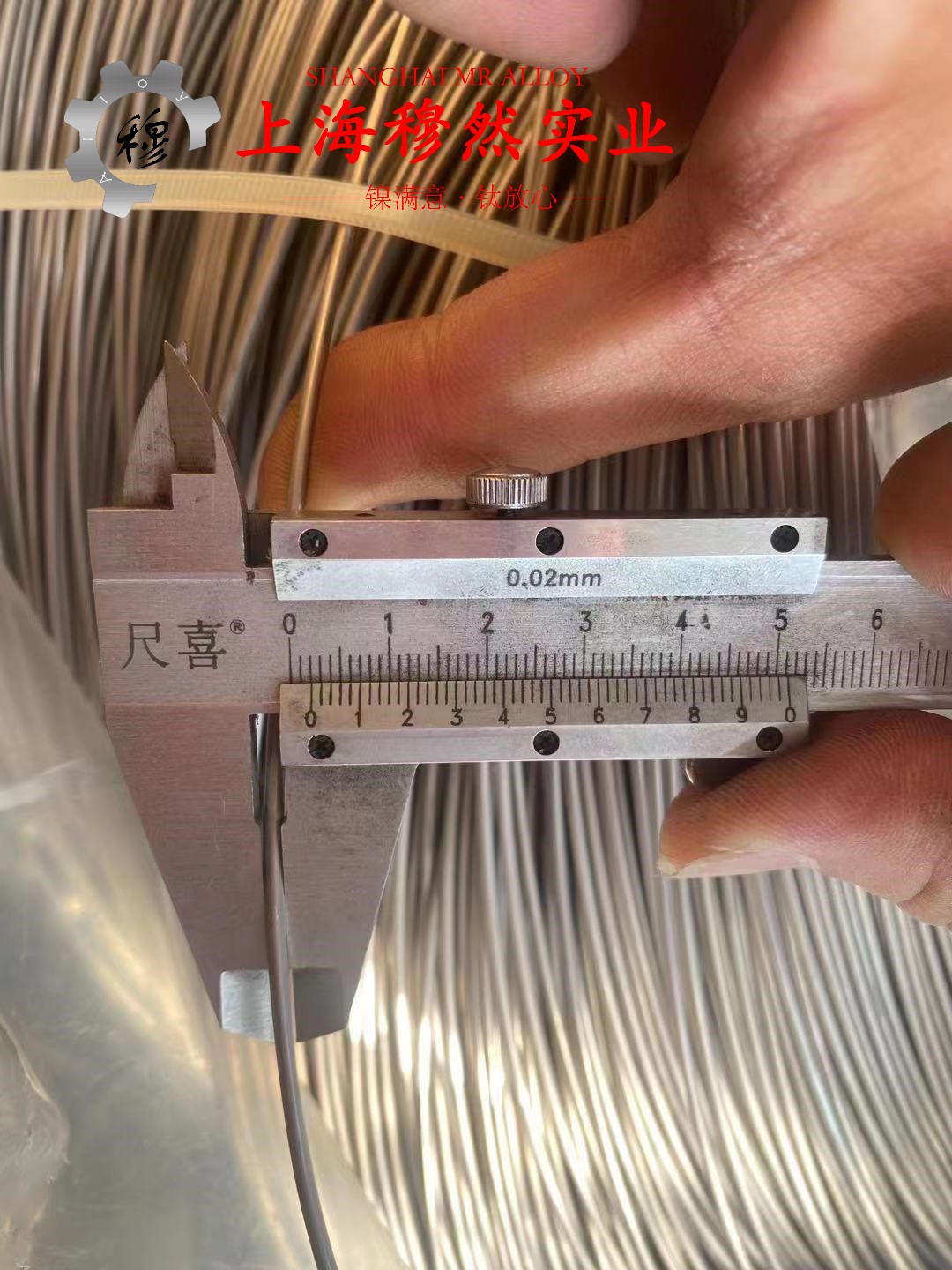