TA8钛合金比TA1硬吗?
钛合金因其优异的物理和化学性能,广泛应用于航空航天、医疗器械、化工设备等领域。在钛合金中,TA系列钛合金备受瞩目。其中,TA8和TA1作为典型代表,常被用于不同的应用场景。TA8钛合金是否比TA1更硬呢?本文将通过分析TA8与TA1的成分、结构、物理性能等多方面,深入探讨这两个合金之间的差异,并最终解答这个问题。
一、TA8与TA1钛合金简介
1. TA1钛合金简介
TA1属于工业纯钛(CP Titanium),是TA系列钛合金中纯度最高的一种,钛含量超过99.5%。作为最纯的钛合金,TA1的特点是具有优异的耐腐蚀性、良好的塑性和韧性,但其硬度和强度相对较低。由于其突出的耐腐蚀性,TA1常用于需要高度抗腐蚀的环境,例如海洋工程、化工设备和医疗器械中。
2. TA8钛合金简介
相比之下,TA8属于钛-铝合金,是α型钛合金,其主要合金元素为铝(6%),含有少量的氧和氢等杂质。这种合金比纯钛更为坚固,具有较高的硬度、强度和耐热性。由于这些特性,TA8钛合金常用于航空航天、发动机零部件等需要高温、高强度的场景中。
3. 为什么硬度重要?
硬度是衡量材料抗压缩、抗穿刺和耐磨损性能的一个重要指标,通常与材料的强度成正比。在工程应用中,硬度直接关系到材料的使用寿命和性能,因此在选材时往往是一个关键的考量因素。
二、TA8钛合金比TA1更硬吗?
1. 组成成分对硬度的影响
成分是硬度差异的核心。TA1钛合金几乎是纯钛,杂质含量极低,虽然有很好的延展性和抗腐蚀性,但钛作为纯金属的本质属性决定了其强度和硬度都比较有限。
相比之下,TA8通过添加6%的铝元素,大幅提高了材料的硬度和强度。铝是一种强烈的固溶强化元素,能够显著提升钛合金的硬度和耐高温性能。TA8中的微量氧和氢杂质也会在一定程度上增加合金的硬度。
结论:由于TA8钛合金中含有的铝元素及杂质对钛基体的强化作用,其硬度自然高于几乎纯钛的TA1。
2. 结构与硬度的关系
TA1钛合金属于纯钛范畴,晶体结构是六方密堆积的α相。这种结构虽然赋予了材料极好的延展性,但相对较低的晶格缺陷密度也限制了其硬度的提升。简单来说,TA1的结构更柔韧,但硬度不足。
TA8钛合金是典型的α型钛合金,其α相通过合金化元素铝的引入,结构更加致密、稳定,晶格结构中的点缺陷、位错密度等增加,整体材料表现出较高的硬度。再加上α型钛合金具有良好的抗蠕变性,在高温下的硬度保持效果优异。
结论:TA8钛合金由于晶体结构的强化,其硬度高于TA1。
3. 物理性能的对比
硬度通常通过维氏硬度(HV)或洛氏硬度(HRC)来测量。根据数据,TA1的维氏硬度为160-200HV,而TA8的维氏硬度则在280-350HV左右。从这些数值可以看出,TA8钛合金的硬度显著高于TA1,差异非常明显。
这种硬度差异带来的实际应用效果也非常突出。TA1适合那些需要高塑性、成形性和抗腐蚀性能的场景,而TA8则更适合高温、高负荷工况,能够承受更大的应力和磨损。
三、硬度的影响因素和应用场景
1. 温度对硬度的影响
TA1由于没有合金元素的强化作用,在高温环境下硬度会迅速下降,其应用场景往往限制在常温或稍高温度的环境下。而TA8由于铝的存在,不仅提高了常温下的硬度,还赋予了其良好的抗高温能力。在航空航天和发动机制造中,TA8经常作为高温零部件的材料。
2. 加工工艺的影响
虽然材料的化学成分决定了合金的基础硬度,但不同的加工工艺也会显著影响材料的最终硬度。对于TA1,通常采用冷轧、热轧等工艺来改善其性能;而对于TA8,热处理和机械加工能够进一步提高其硬度和耐磨性。
四、结论
通过对TA1和TA8钛合金的成分、晶体结构、物理性能以及应用场景的深入分析,可以明确得出结论:TA8钛合金比TA1更硬。这主要归功于TA8中添加的铝元素以及微量杂质对材料基体的强化作用,使得TA8在强度、硬度和高温耐受性上都明显优于TA1。而TA1作为几乎纯钛的代表,其主要优势在于高塑性和优异的耐腐蚀性,适合那些不需要高硬度但要求材料具备良好抗腐蚀性能的场合。
在实际选材过程中,硬度并非唯一决定因素,还需综合考虑材料的韧性、延展性、耐腐蚀性等性能。如果你需要在高温、高强度环境下使用材料,TA8会是更好的选择;而在耐腐蚀、对硬度要求不高的场景中,TA1则是更优解。
最后一句话总结
TA8硬度的提升意味着其在应用中具有更强的耐用性,但也意味着其加工和成本可能更高,因此合理的应用选择至关重要。
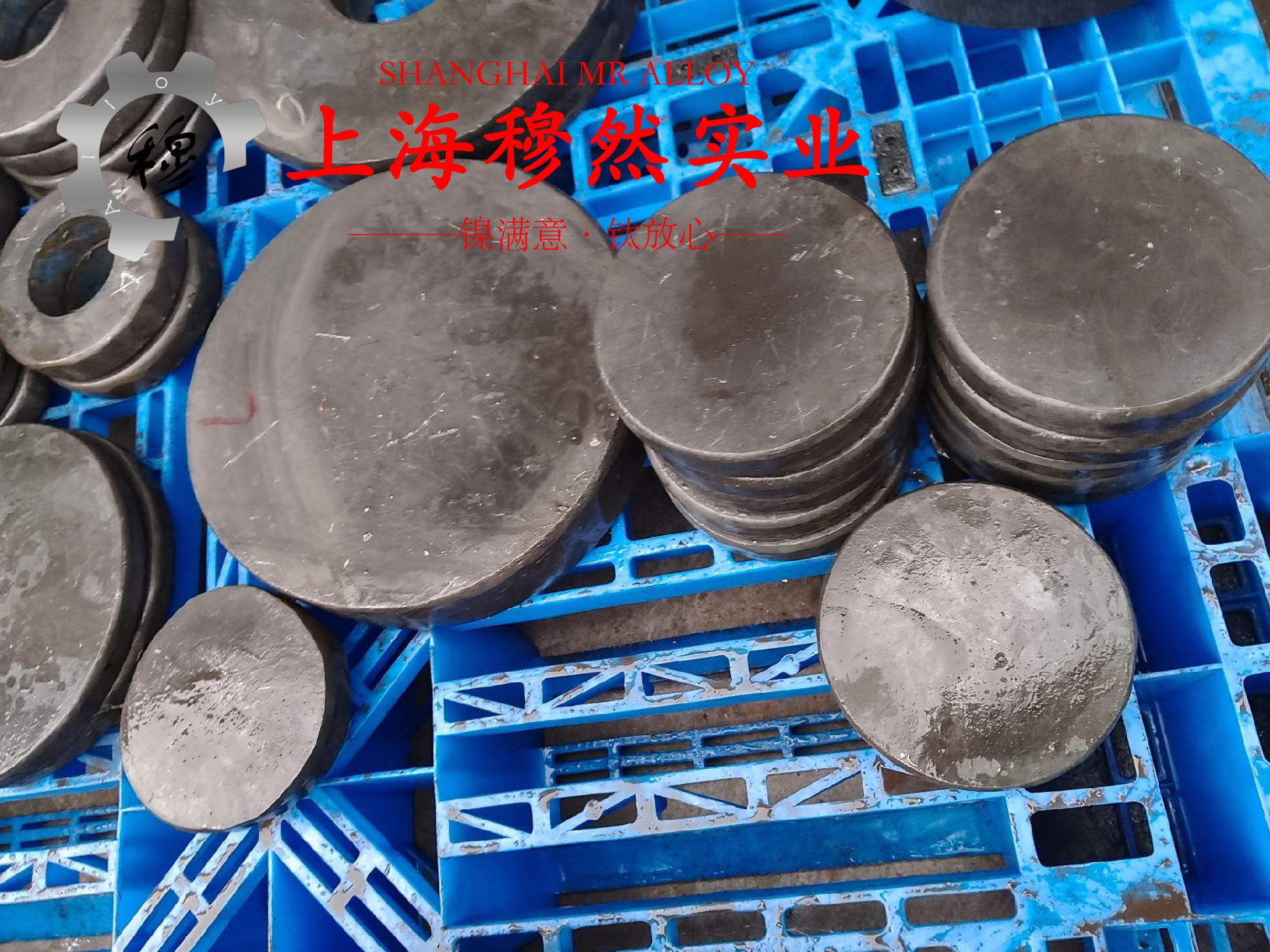
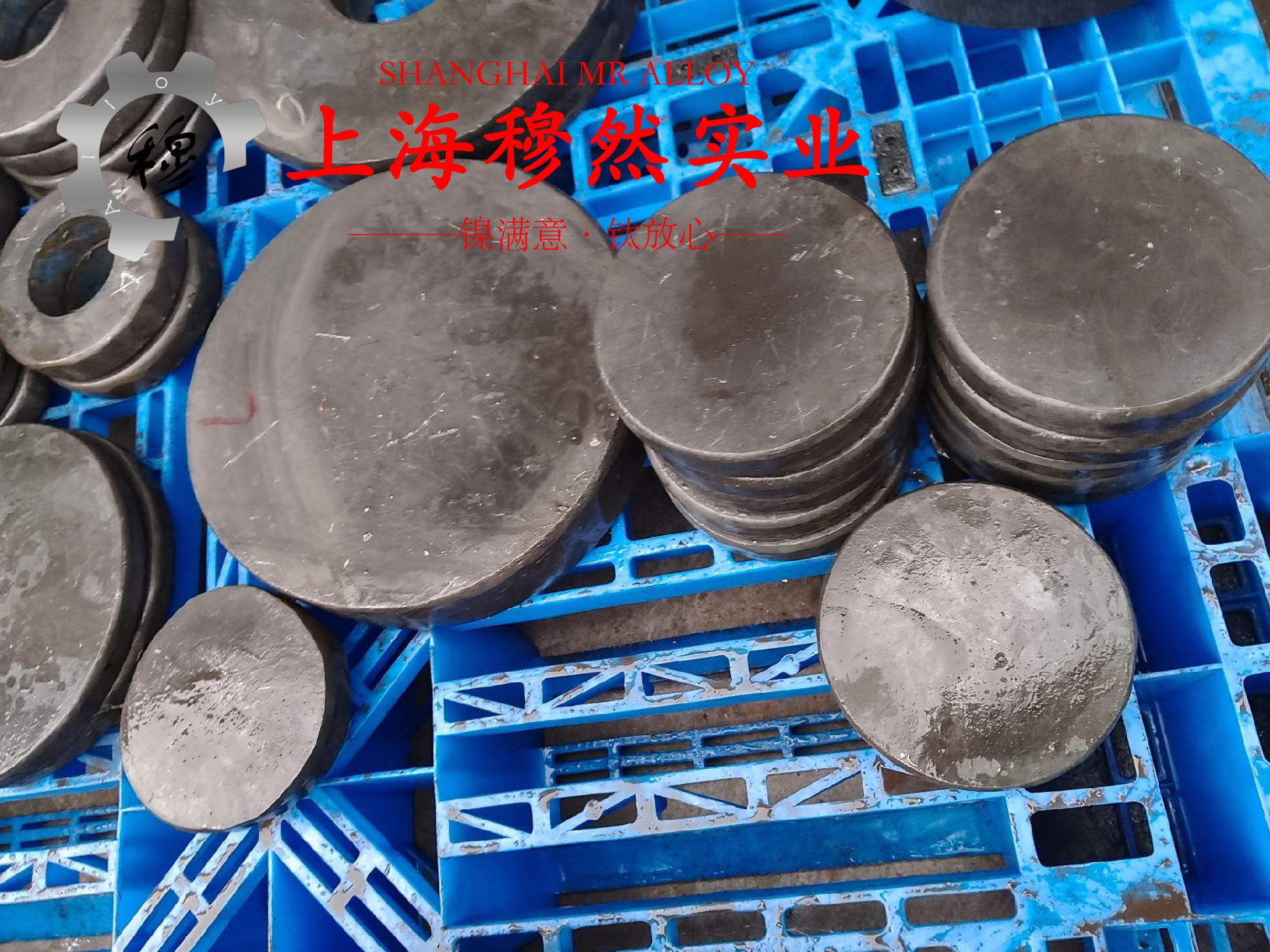