UNSN02201镍合金是应用广泛的高性能合金材料,尤其在航空航天、化学工程和高温环境中展现出卓越的抗腐蚀性和高温稳定性。这种优异的特性也让它在加工过程中遇到了一些挑战。尤其是在切削加工和磨削过程中,如何有效提高加工精度、延长刀具寿命,并确保加工质量,是众多制造业工程师和技术人员面临的重要问题。
1.UNSN02201镍合金的基本特性
UNSN02201镍合金是一种主要由镍元素组成的合金材料,具有很高的抗腐蚀能力,尤其是在酸性和氯化物环境中表现尤为突出。它在高温下具有较好的稳定性,能够承受高达1000°C的温度。因此,UNSN02201广泛应用于航空航天、化学反应器以及海洋工程等领域。正因为其良好的抗腐蚀性和耐高温特性,导致其在加工时相较于普通金属具有更高的切削难度。
2.切削加工挑战与应对
UNSN02201镍合金具有较高的强度和硬度,使得其在切削加工过程中容易产生较大的加工热量,进而导致刀具的磨损加剧。合金的低热导性也导致热量无法有效散发,进一步增加了加工难度。为了克服这些问题,采取合适的切削条件显得尤为重要。
合理选择刀具材料至关重要。由于UNSN02201合金具有较高的硬度,因此需要选用具备较高耐磨性的硬质合金或陶瓷材料作为切削工具。切削速度和进给量的控制也非常关键。较低的切削速度有助于减轻刀具的磨损,同时通过适当增加切削进给量,可以有效提高生产效率。更为重要的是,切削液的使用不可忽视。高效的切削液不仅能够冷却刀具,还能够减少切削区的摩擦力,从而降低刀具温度,延长其使用寿命。
3.切削加工方法的选择
在切削加工方法的选择上,精密车削、铣削、钻削等技术通常能够应用于UNSN02201镍合金的加工。但是,由于合金的加工硬化特性,采用适合的切削路径和刀具角度对于保证加工质量十分重要。对于一些复杂的加工要求,可以考虑采用更精细的数控机床进行加工,以确保加工的精度和表面质量。
4.提高刀具寿命与加工精度
为延长刀具的使用寿命,除了上述的切削条件控制外,还可以考虑在加工过程中进行定期的刀具检查和替换,防止刀具磨损过度而影响加工精度。使用高品质的刀具和优质的切削液,也能有效减少磨损和提高切削效率。
5.UNSN02201镍合金的磨削性能分析
除了切削加工外,UNSN02201镍合金在磨削加工中也面临一定的挑战。磨削是对工件表面进行精加工的重要方式,尤其是在高精度加工中占据了重要地位。由于其硬度较高、强度较强,磨削时容易出现热影响区、工件表面粗糙度较大等问题。
在磨削加工过程中,合金的硬度和高温稳定性使得磨削变得更加困难。为了克服这些挑战,选用合适的磨具和磨削参数同样至关重要。常见的磨削方式包括平面磨削、圆周磨削等,对于UNSN02201镍合金而言,通常需要采用高性能的金刚石或CBN(立方氮化硼)磨具。这些磨具具有极高的硬度和耐磨性,可以有效减少磨削过程中产生的热量,避免对工件表面造成过多的热影响。
6.磨削过程中温度控制
磨削过程中的温度控制同样是提高加工精度和减少热影响的关键。高温会导致工件的表面质量下降,并可能导致工件变形或产生裂纹。因此,在磨削过程中,需要使用足够量的冷却液,以确保磨削区的温度不会过高。冷却液不仅能有效带走热量,还能清除磨削过程中的切屑,减少磨粒堵塞和刀具损坏的可能性。
7.磨削工艺的优化
为了提高UNSN02201镍合金的磨削性能,技术人员通常会选择优化磨削工艺。例如,通过调整磨削速度、进给量以及切削深度等参数,找到最佳的磨削条件。合理的工件夹持方式和精确的磨削机床控制也有助于提高加工的稳定性和表面质量。
在磨削过程中,工件的表面质量至关重要。对于UNSN02201合金材料来说,表面粗糙度的控制尤其重要。通过精细的磨削工艺,可以获得较为光滑的表面,进而提高合金在实际应用中的耐腐蚀性和耐高温性能。
8.小结:切削与磨削的协同优化
UNSN02201镍合金的切削加工和磨削加工都具有一定的难度,但通过科学的工艺选择和技术优化,可以有效提高加工效率和表面质量。切削加工中合理控制切削条件、选择合适的刀具和切削液,可以大大提高加工效率;在磨削过程中,合理的磨削工艺和温度控制则有助于提高表面质量,延长刀具寿命。通过这些优化措施,不仅能够提高加工精度,还能延长设备使用寿命,减少生产成本,为制造业带来更高的生产效益。
UNSN02201镍合金在切削与磨削加工中的挑战并非无法克服。随着技术的进步与设备的不断提升,更多高效、精密的加工方式和工艺将不断涌现,为该合金的加工应用提供更多的解决方案。
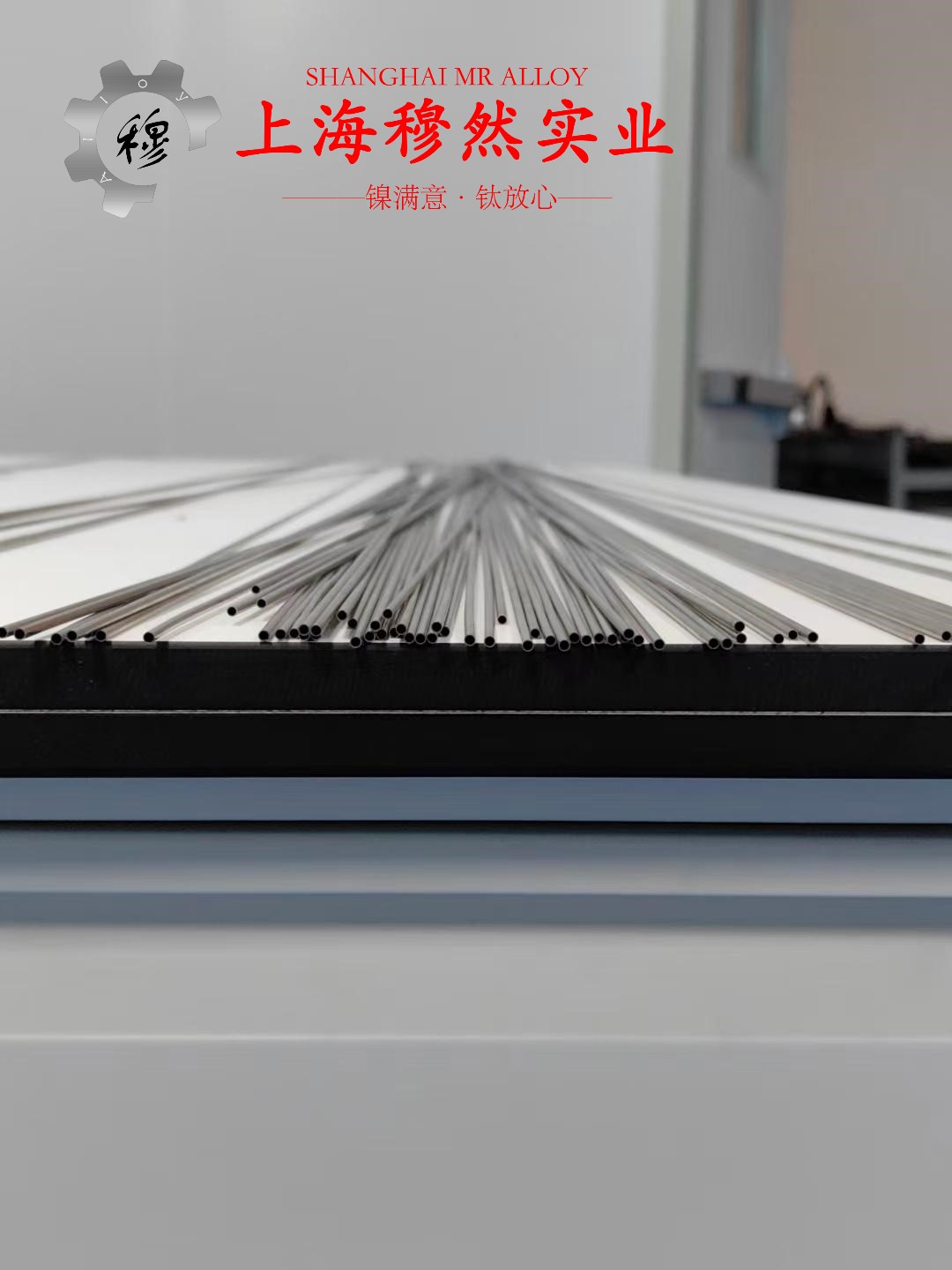
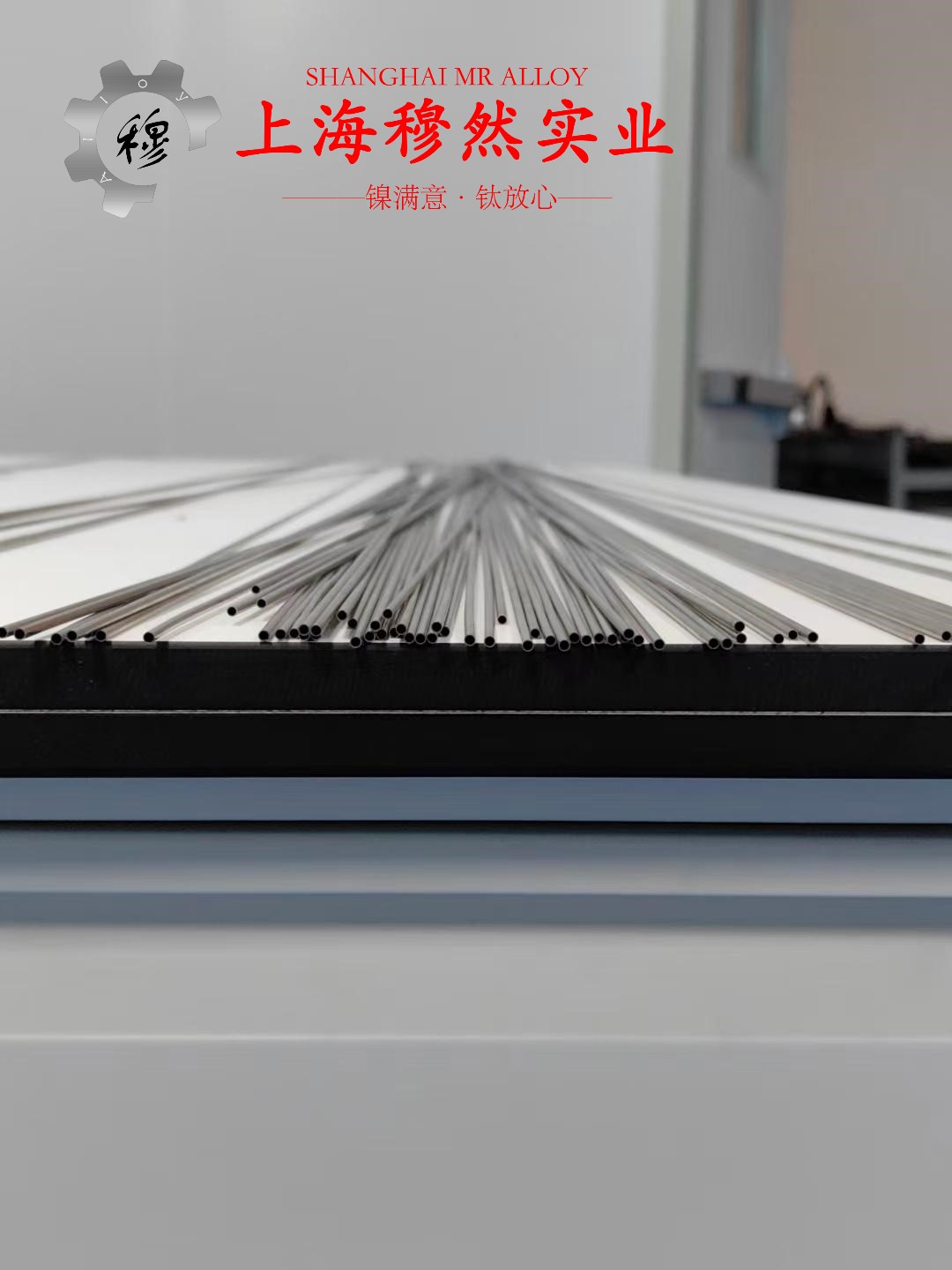