CuNi44 (NC050) 铜镍电阻合金冶标的疲劳性能综述
引言
铜镍电阻合金(CuNi合金)在现代电子、电气及航天等行业中具有重要应用,尤其是在电阻材料的制造方面。CuNi44(NC050)合金作为一种具有高电阻率和优良机械性能的铜镍合金,广泛应用于电阻元件、传感器及精密仪器中。在实际应用中,CuNi44合金常常暴露在长期动态负载条件下,导致疲劳损伤。因此,研究其疲劳性能对于提升其使用寿命及可靠性具有重要意义。本文将综述CuNi44合金的疲劳性能研究现状,并分析其影响因素及改进途径,为相关领域的科研工作者提供参考。
CuNi44合金的基本特性
CuNi44合金的主要组成元素为铜和镍,其中铜的质量分数约为56%,镍的质量分数为44%。这种合金的电阻率较高,具有较好的抗氧化性和耐腐蚀性能,常用于精密电阻器、热电偶材料以及高稳定性电气元件。其较高的电阻率和热稳定性使其在高温和高负载环境下仍能保持稳定的电性能。由于其含有大量的镍元素,合金的力学性能和疲劳性能受到显著影响。
疲劳性能的影响因素
CuNi44合金的疲劳性能受多个因素的影响,包括材料的微观结构、应力集中、环境因素以及加载方式等。材料的微观结构对疲劳性能有着直接的影响。CuNi44合金通常具有细小的晶粒结构,能够在一定程度上提高合金的强度和抗疲劳性能。合金中可能存在的相界面或析出物会在高应力作用下成为疲劳裂纹的源头,降低其疲劳寿命。
合金表面质量和应力集中效应是影响疲劳性能的关键因素。表面缺陷、划痕、孔洞等都会成为局部应力集中的部位,进而引发疲劳裂纹的形成。对于CuNi44合金而言,其表面处理工艺,如热处理或表面涂层,能够显著改善其抗疲劳性能。
环境因素也对合金的疲劳性能产生重要影响。例如,在高温、腐蚀性环境下,CuNi44合金的疲劳寿命往往会大幅下降。高温会导致材料的应力-应变行为发生变化,降低其抗疲劳性能;而腐蚀性环境则可能加速裂纹的扩展,进一步降低材料的使用寿命。
疲劳性能研究现状
近年来,关于CuNi44合金疲劳性能的研究主要集中在两个方面:一是其在不同加载条件下的疲劳特性;二是通过改进合金成分和制造工艺来提高其疲劳寿命。
关于加载条件的研究表明,CuNi44合金在高频疲劳测试中表现出较好的疲劳性能,但在低频疲劳条件下,由于热效应和塑性变形的累积,疲劳寿命明显下降。研究者通过实验表明,CuNi44合金在温度较高时,其疲劳极限和疲劳寿命会出现显著的降低,这提示在高温环境下,合金的疲劳性能需要特别关注。
在合金成分改进方面,研究人员尝试通过调节合金的镍含量、加入微量元素(如铬、钼等)来优化CuNi44合金的疲劳性能。研究表明,适量添加铬或钼能显著改善合金的抗疲劳性能,尤其是在高温环境下。采用不同的热处理工艺,如退火、固溶处理等,也可以有效地改善CuNi44合金的微观结构,从而提高其疲劳性能。
疲劳损伤机制与分析
CuNi44合金的疲劳损伤机制较为复杂,通常表现为疲劳裂纹的初始萌生、扩展及最终断裂。在低应力水平下,疲劳裂纹的萌生多发生在合金的界面或夹杂物处;而在高应力水平下,裂纹往往首先出现在表面缺陷和晶界区域。裂纹的扩展过程通常表现为逐步的塑性变形,并伴随着材料的应力松弛现象。最终,合金可能发生脆性断裂,导致性能的急剧下降。
为了有效地预测CuNi44合金的疲劳寿命,许多研究采用了基于断裂力学的疲劳寿命预测模型。这些模型能够通过对材料微观结构的深入分析,揭示出疲劳裂纹萌生和扩展的关键因素,并为合金的疲劳性能优化提供理论依据。
结论
CuNi44(NC050)铜镍电阻合金具有优异的电气性能和良好的机械性能,但其疲劳性能在实际应用中仍面临诸多挑战。疲劳性能的提高可以通过优化合金成分、改善制造工艺以及加强表面处理等方式实现。环境因素、加载方式和微观结构的影响同样不可忽视。未来,针对CuNi44合金疲劳性能的进一步研究,应聚焦于疲劳损伤机制的深入探讨以及高效的疲劳寿命预测模型的建立,为其在更广泛的工程应用中提供理论支持与实践指导。
通过提升CuNi44合金的疲劳性能,将能够延长其使用寿命,提升产品的可靠性,为电子、电气等高技术领域的创新发展提供更加坚实的材料基础。
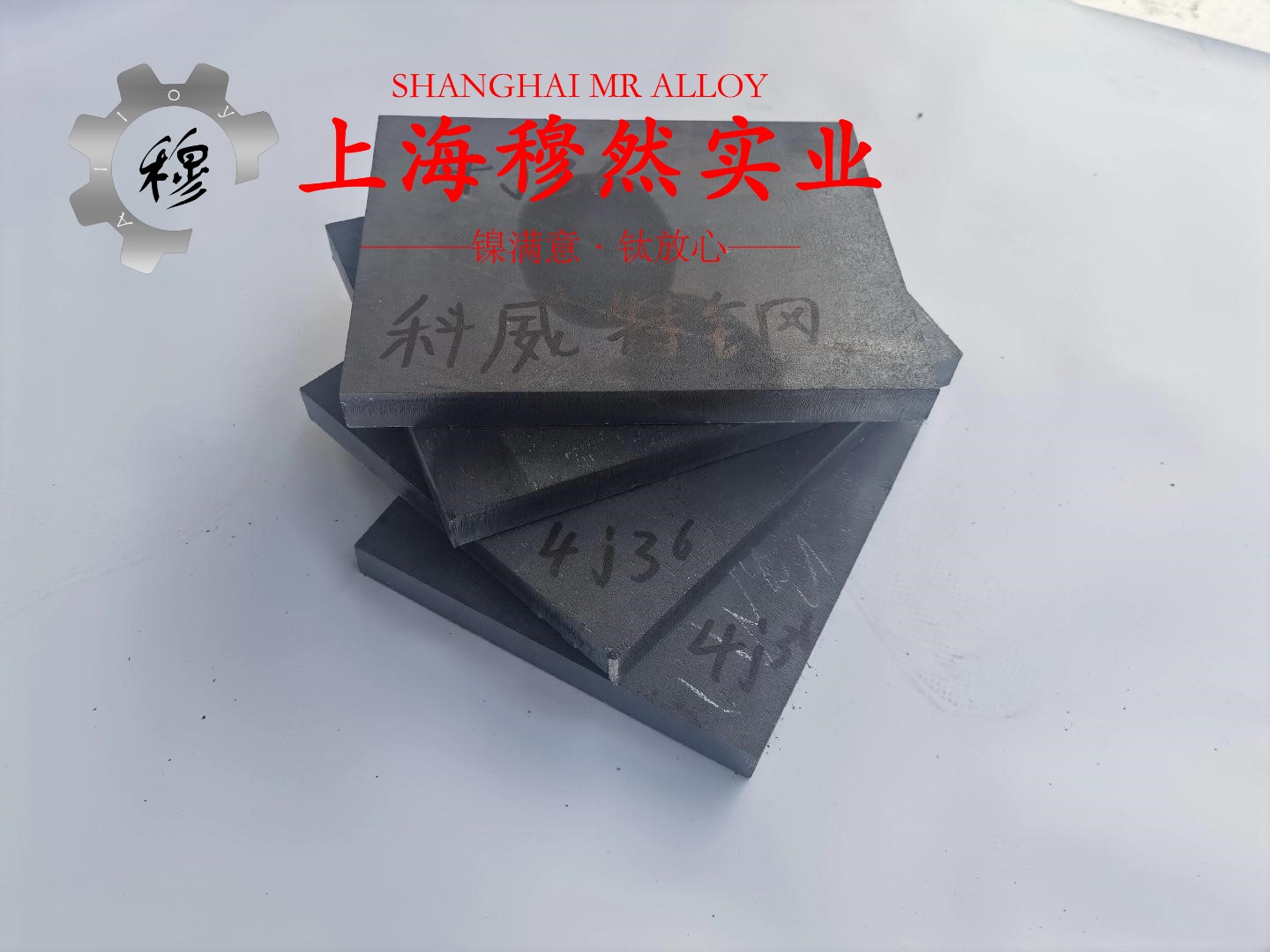
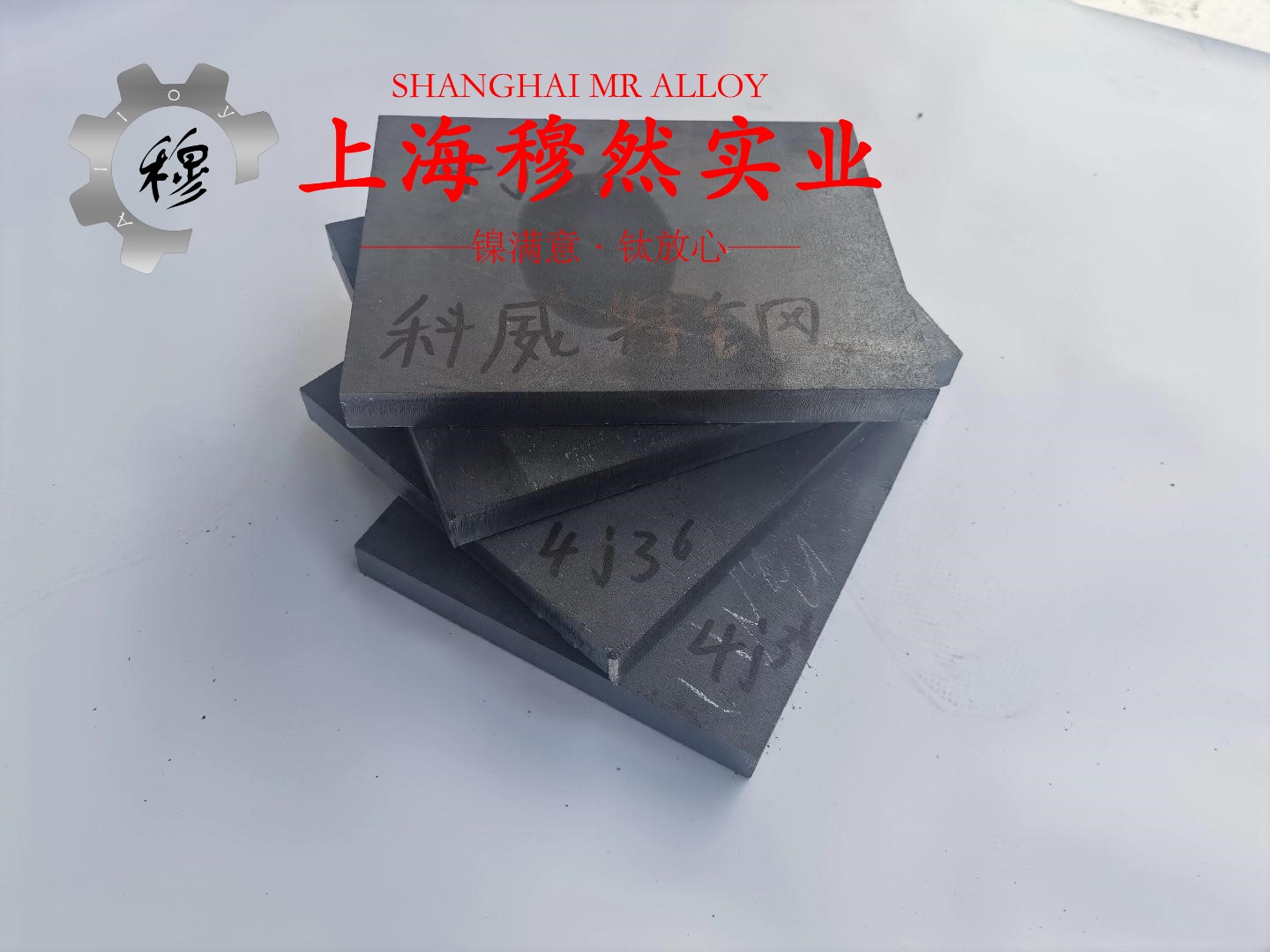